Two Lessons to Learn from the Recent Heat Wave
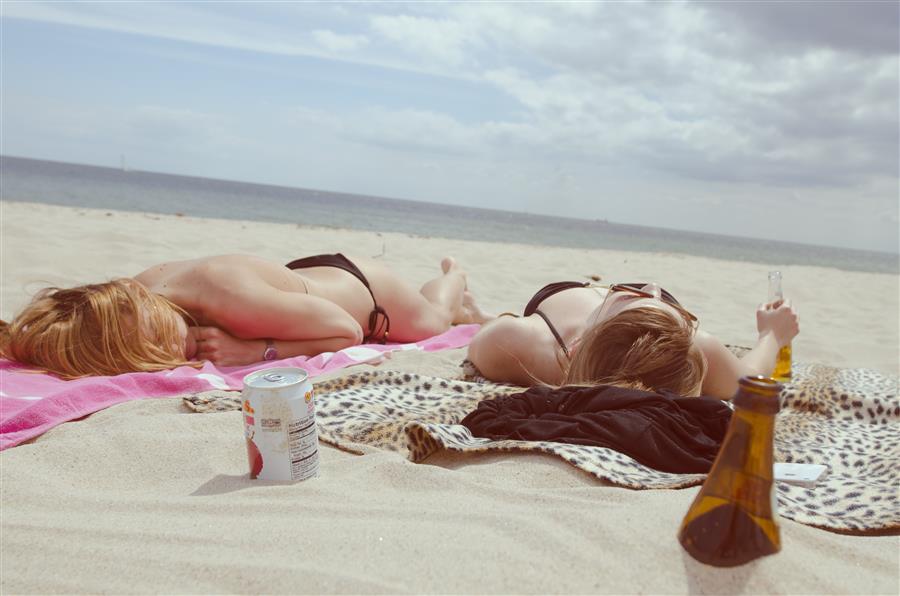
A severe heat wave that hit the UK in 2003 led to massive refrigeration failures in a variety of different industries. Hardest hit were supermarkets that found themselves completely unprepared without adequate backup refrigeration or resources to get their failed units back online. One would think we would have learned from the events of 12 years ago. Apparently not. The recent heat wave we just experienced resulted in the same kinds of failures. Whether supermarket coolers or walk-in cold rooms, the country’s equipment just could not withstand the heat.
So, what do we do? The most recent heat wave is certainly not the last one we will experience. How do we do a better job of being prepared next time? By paying attention to two crucial lessons we can, and should, learn as a result of the soaring temperatures of a few weeks ago.
1. Temporary Emergency Refrigeration Should Not Be Ignored
At data centres, you will find backup generators ready to kick into action in the event of a power failure. The best data centres also keep extra equipment on hand just in case something fails. Throughout numerous industries, it is easy to observe redundancy built into systems in order to quickly recover from emergencies. Why is the same thing not valid for refrigeration?
A restaurant, supermarket, or medical facility does not necessarily need to keep a refrigerated trailer or walk-in cold room on-site as a backup. However, any industry relying on refrigerator and freezer capacity for daily operations should have a system in place to access temporary refrigeration at a moment’s notice. At Icecool Trailers, we have a number of clients who retain us as their emergency refrigeration provider at all times. If they have a problem, they know they can call us for immediate emergency service.
Having temporary refrigeration established ahead of time would have made it possible for some of our supermarkets to keep at least a basic stock of refrigerated goods while they waited for repair crews to come and fix failed refrigerators and freezers. It would also have prevented the food waste resulting from spoilage.
{module_webapps,1841,i,182141}
Better Maintenance and Repairs
The second lesson to be learned is that there is a definite need for improved maintenance and repair schedules. Fridge Hub's Simon Randell, a refrigeration specialist whose company provided service and maintenance contracts when the 2003 heat wave hit, said in a recent blog post that companies are not putting enough resources into maintaining their current equipment. He says more resources have to be invested in both personnel and hardware.
No refrigeration unit will work for its entire life without experiencing some sort of mechanical failure. Nevertheless, mechanical failures can be kept at a minimum through an effective maintenance strategy that takes care of basics so that minor problems do not become major disasters.
Icecool Trailers cannot do anything to help our clients improve the maintenance and repair schedules of their in-house equipment. We can provide temporary emergency refrigeration by way of trailers and walk-in cold rooms with just one phone call. We take pride in our two-hour service in the Greater London area, and same-day service in other parts of England and South Wales.
We invite you to contact us to learn more about our trailers and walk-in rooms. We provide several sizes of each, for both refrigeration and freezing. Whether you need a refrigerated trailer for an outdoor event or a walk-in freezer for interior storage, we have the quality equipment you need backed by reliable service.
Sources:
1.Fridge Hub – http://fridgehub.com/category-uk-news