How Does a Refrigerated Trailer Work
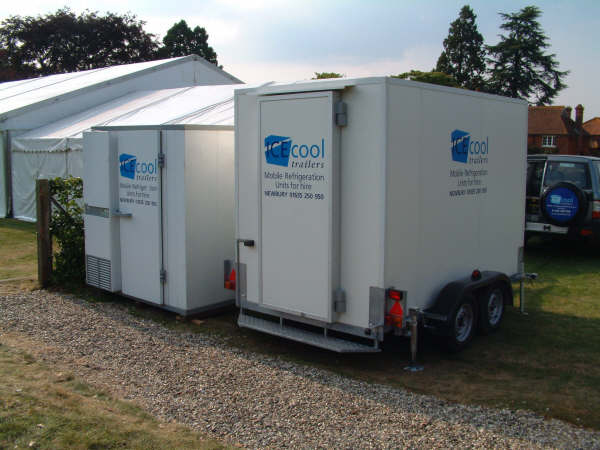
In today's globalised world, the ability to transport perishable goods over long distances is crucial for businesses across a range of different industries. From fresh produce and pharmaceuticals to chemicals and electronics, many products require strict temperature control to maintain their quality and safety during transit. This is where refrigerated trailers come into play - these specialised vehicles are designed to create a mobile cold storage environment, ensuring that sensitive cargo reaches its destination in perfect condition. But how do they work? In this blog post, we'll explore the fascinating technology behind refrigerated trailers and discover how they work to keep our goods fresh on the road. Let’s dive in.
What are Refrigerated Trailers?
Refrigerated trailers, also known as reefers, are essential for transporting perishable goods across long distances. These specialised trailers are designed to maintain a consistent temperature range, ensuring that sensitive cargo remains fresh and safe during transit. So how exactly do these mobile refrigeration units work? Let's take a closer look at the technology behind refrigerated trailers.
And if you’re looking for a chiller trailer hire in the UK, don’t hesitate to contact us for a quote.
How Do Refrigerated Trailers Work?
Refrigeration in a chiller trailer is achieved in the same way it is a household fridge.
The trailer is hooked up to a power supply, in our case either a 13-amp or 16-amp power supply or a portable generator delivering the same output. Electricity powers a motor and compressor hidden away in the trailer, while the compressor squeezes an eco-friendly refrigeration gas called HFC-134a, or tetrafluoroethane (Freon), and this compression causes it to liquefy. Once it is in liquid form and at a high pressure, the refrigerant absorbs heat inside the trailer, cooling down the air to reduce the ambient temperature.
The refrigerant constantly evaporates back into a gas, where it flows back to the compressor, and the cycle starts over again.
Temperature Control Mechanisms
Refrigerated trailers are also equipped with advanced temperature control systems that allow operators to set and maintain specific temperature ranges. These systems typically include a thermostat, which monitors the trailer's interior temperature and sends signals to the refrigeration unit to adjust its output accordingly. Some trailers also feature multiple temperature zones, allowing for the simultaneous transport of goods requiring different storage conditions.
Insulation and Sealing
To maintain the desired temperature, refrigerated trailers are constructed with high-quality insulation materials, such as polyurethane foam, which minimises heat transfer between the interior and exterior environments. The trailer's doors are also designed with tight seals to prevent air leakage and maintain temperature stability. Proper insulation and sealing are crucial for ensuring the efficiency of the refrigeration system and protecting the cargo from temperature fluctuations.
Power Sources
Refrigerated trailers require a reliable power source to operate their cooling systems. Most trailers are equipped with diesel-powered generator sets, which provide electricity to run the refrigeration unit independently of the truck's engine. Some newer models also feature electric standby options, allowing them to be plugged into an external power source when parked at a facility, saving fuel and reducing emissions.
Monitoring and Maintenance
To ensure optimal performance and prevent costly breakdowns, it’s a good idea to ensure you engage in regular monitoring and maintenance for your chiller trailer. Many modern trailers are equipped with telematics systems that provide real-time data on temperature, humidity, and location, enabling fleet managers to monitor their cargo remotely and respond quickly to any issues. Regular servicing, including cleaning the condenser coils, checking the refrigerant levels, and inspecting the insulation, helps to maintain the trailer's efficiency and extend its lifespan.
Final Thoughts
Ultimately, refrigerated trailers are complex machines that play a vital role in the cold chain logistics industry; whether you're shipping fresh produce, pharmaceuticals, or other temperature-sensitive products, a well-maintained refrigerated trailer is essential for protecting your cargo and your bottom line. To learn more about the benefits of hiring refrigerated trailers, visit our website and discover how our state-of-the-art fleet can support your business needs.
FAQs
How do freezer trailers work?
Refrigeration in a freezer trailer works in the same way as a chiller trailer, except it can be set to a far lower ambient temperature range. This requires a special compressor that can compress gas to a high enough pressure to maintain a temperature of at least - 18° C.
What are the refrigeration components made from?
The refrigeration components are made of aluminium, copper, or an alloy, while the walls are made of plastic (moulded polyurethane and polystyrene) and these keep cool air inside the trailer. The ambient temperature can be controlled by switching quickly and easily.
Who are chiller trailers and freezer trailers for?
Although most of our customers operate in the food and drink industry, we also readily supply chiller and freezer trailers to the medical industry. Our trailers are also available for disaster recovery and to cope with an uptick in produce demand during seasonal periods, so really, anybody can benefit from temporary refrigeration with a chiller trailer.